Highlights
- Leveraging advanced analytics is one of the leading smart water opportunities for water and wastewater utilities to improve operational intelligence.
- “Used effectively, advanced analytics can predict equipment failure and process outcomes, help develop reliable maintenance schedules, and save time and money across an entire operation.”
- Data-driven models are agile and are therefore more amenable to being used for real-time optimization and operationalizing.
What is pricey and plentiful at wastewater utilities but not put to use effectively? Data.
Without proper optimization in place, the power of that data to identify and implement efficiencies, address process issues, and cut down on costs remains buried in an ever-growing pile of siloed ones and zeroes. That’s why leveraging advanced analytics is one of the leading smart water opportunities for water and wastewater utilities to improve operational intelligence.
“Used effectively, advanced analytics can predict equipment failure and process outcomes, help develop reliable maintenance schedules, and save time and money across an entire operation.”
Brown and Caldwell (BC) National Analytics Engineering Lead Jamie Lefkowitz
Dr. Varun Srinivasan, a Brown and Caldwell Process Engineer and Data Scientist, agrees, adding: “There is no question that we have a lot of data at the plant stored in disparate data silos, but most of it is barely used. Any use that the data gets is in manual spreadsheets that operators put together to track plant performance. This takes a lot of time and effort. We want to take the data and transform it from disconnected systems and time-consuming manual spreadsheets to a secure single database with an intuitive dashboard for the user to see what’s happening now, what’s happened in the past, and perform advanced analytics to optimize the facility’s processes.”
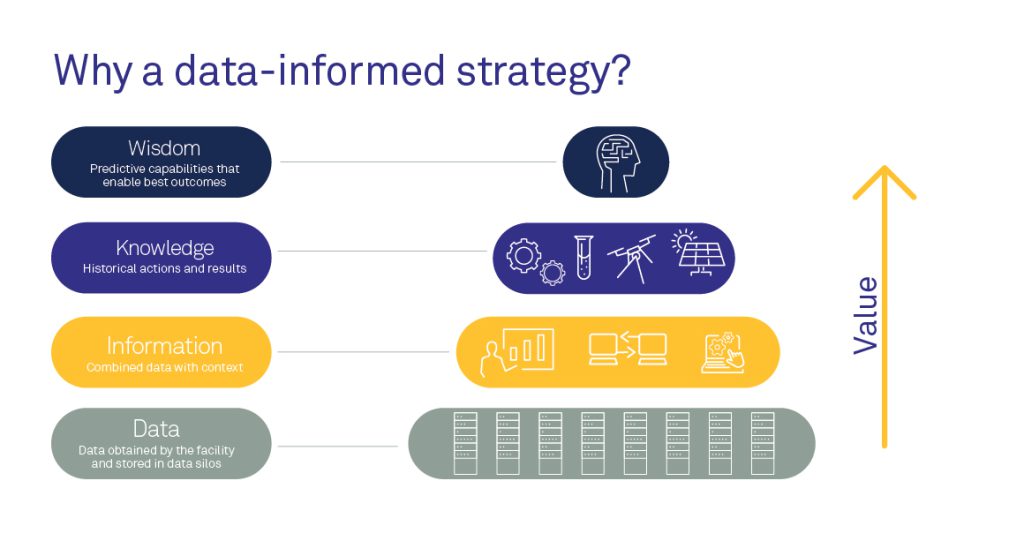
Figure 1
4 reasons to switch
There are four main reasons to switch to an advanced analytics data-informed strategy (Figure 1):
- Utilities are already spending money on generating data. The cost of this endeavor is compounded by underutilized data.
- Data-driven models can be used to fill in gaps for calibrated process models and vice-versa.
- Data-driven models are agile and are therefore more amenable to being used for real-time optimization and operationalizing.
- Machine learning algorithms are especially adept at detecting layered process interactions that are challenging to represent with deterministic models. For instance, in traditional process optimization, biological process models lack hydraulics representation. However, a machine learning algorithm could potentially account for both hydraulic and biological mechanisms by learning from the data.
“So, if you have data missing,” Dr. Srinivasan explains further, “you can have data-driven models and process models generating synthetic data, what we call ‘soft sensors,’ what should be ammonia for example based on all the things that are happening, and we can use that to inform your analytics in many ways. These soft sensors can also be used to determine if sensors are performing appropriately and if they need maintenance/calibration. This helps promote sensor trust and adoption.”
How does it work? Simply put, the implementation follows a simple 1-2-3 process:
- Gather data
- Store data in a secure, one-way singular database
- Analyze data
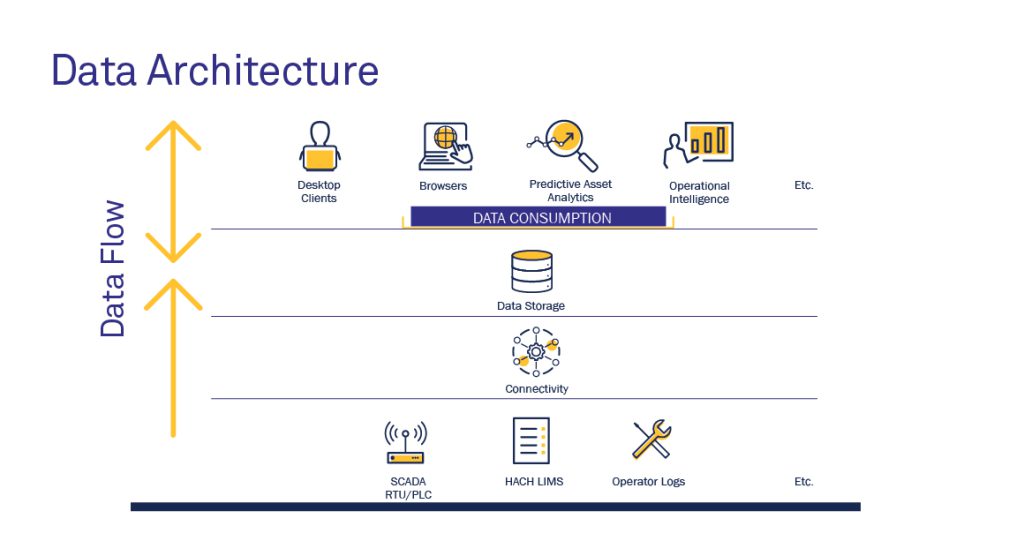
Figure 2
Cybersecurity
Before Step 1 can commence, the data must be secure.
To address security concerns, BC utilizes a one-way data flow architecture (Figure 2) in which there is only data output but no write-back to a utility’s control system or network.
“We store the data in a way so there’s no communication back to the control system. All the data from different systems such as SCADA, LIMS, and logs only goes into the database and there is no control access back into the operations systems. There is minimal concern with someone accessing it externally,” Dr. Srinivasan says. “We need to build trust. Many operators don’t even trust a simple proportional-integral-derivative (PID) controller yet so to get them to a point where they can trust what’s happening on a computer, we have to build trust.”
Time series analysis tools
Once a utility’s data is securely connected and integrated, advanced analytics can assist operators with:
- Monitoring: What is happening?
- Summarizing: What happened?
- Diagnostics: Why did it happen?
- Prediction: What will happen?
- Prescription: What should happen?
To achieve these results, BC uses time series analysis tools that can be connected to data repositories such as SCADA historians and lab databases.
“Even though there’s all this coding going on in the backend, for the user, it’s all point and click. You say, ‘I want to clean this data,’ then boom, outlier removal. You say, ‘I want to do some linear regression modeling, identify reference profiles over 20 years of data,’ it will identify all of them. It’s all point and click. That is the beauty of it,” Dr. Srinivasan says.
Case study: Dynamic dosing
A successful case in point is an East Coast utility’s challenge with ferric dosing (Figure 3). The utility runs an extremely complicated plant that experiences a lag between change in ferric dosing and effluent phosphorus concentration. The challenges included:
- Complex process and timing of dosing was difficult to calculate.
- Auto-correlation of effluent orthophosphate (OP) with historical effluent OP.
- Multiple dosing locations.
- Weekly as well as monthly stringent phosphorus limits.
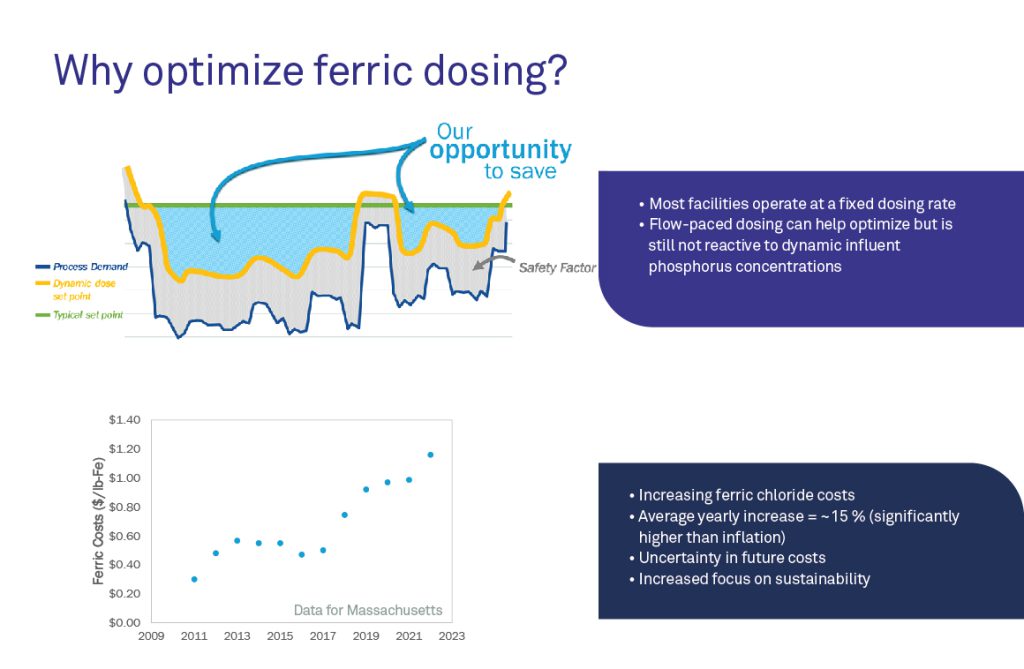
Figure 3
The utility and BC team quickly realized that flow-paced dosing can help optimize but cannot react to changing influent phosphorus concentrations. The utility was also facing pressure from rising ferric chloride costs, 15% over last year, cost uncertainty, while wanting to also increase sustainability measures. This is also true for many other chemicals that are being used currently by utilities across the United States.
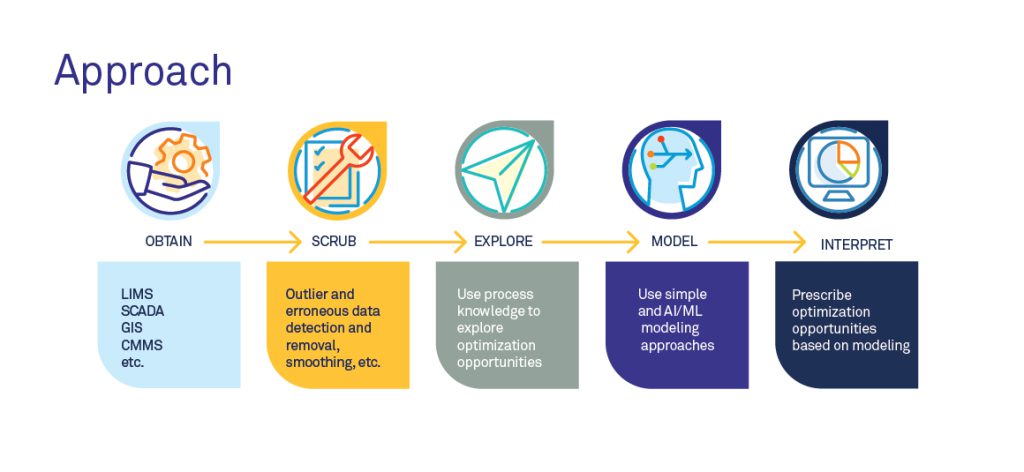
Figure 4
Results: Meet BC:Opta™
By leveraging a unique and proven optimization process (Figure 4), BC was able to help the utility compare different modeling approaches to predict effluent OP with a forecasting period of three days using predictive variables based on plant staff and expert input. Results: The utility was able to easily identify the best effluent phosphorus prediction model using linear regression that will enable a more dynamic dosing paradigm.
“This optimization process takes in the data, process knowledge and subject matter expertise, and converts it into knowledge and then wisdom. We take the data from potential value to actual value by leveraging it to its fullest extent.”
Dr. Varun Srinivasan, BC Process Engineer and Data Scientist
That’s what makes Brown and Caldwell’s approach to optimization, BC:Opta™, so unique. It goes beyond the data to combine people + technology + adoption.
“An optimization approach that recognizes that people and adoption are just as important as the technology has the most chance of success. You need to talk to everyone — engineers, operations, administration — to see what do they need and how do they use it,” Lefkowitz says.
The future
A data-informed strategy powered by advanced analytics can help wastewater utilities gather, clean, and analyze their disjointed data to optimize operations to make the most of their resources, people, and investments and build for the future.
Though we don’t really know with certainty what will come next, Dr. Srinivasan says, “we do know regulations change, goals and objectives shift, and smart water optimization tools like BC:Opta provide solutions. We could train a Digital Twin to do a multi-objective optimization to meet complex goals such as operations and ESG (environmental, social and governance) while meeting complex permit requirements. That’s exciting for all the stakeholders such as communities, operators, and utilities.”