For wastewater treatment facilities (WWTFs), thermal drying of biosolids has emerged as a solution to address risks and leverage beneficial reuse opportunities. That’s because across the country, WWTFs are facing more emerging contaminants such as PFAS and the ensuing more stringent regulations, rapidly rising landfill and end use costs, and growing waste streams.
In this evolving and uncertain market, facilities are looking at upstream solids improvements and downstream technologies to process the biosolids into other valuable products. By making the most out of less waste, thermal drying does both.
What is thermal drying?
Thermal drying is the use of heat — either direct (convection) or indirect (conductive) — to evaporate water from biosolids, typically reducing water content to 10% or less. Thermal drying also produces a low-odor, pathogen-free, and nutrient-rich Class A biosolids product.
Benefits
Thermal drying not only addresses waste management challenges, but also contributes to resource recovery and promotes an eco-friendlier approach to wastewater treatment byproduct utilization:
Reduced cost and risk: By reducing the mass of the waste by four to five times, the need and associated cost for transportation and disposal is greatly reduced. While WWTFs can’t control the fluctuating and rising landfill and fuel costs, the amount of waste to be disposed can be controlled, reducing financial risk in uncertain times.
Beneficial reuse: Because the resulting dried biosolids are typically categorized as Class A, they can be utilized for a more diverse array of beneficial reuse opportunities. This includes non-agricultural opportunities such as fertilizer blending or land reclamation for urban areas with dwindling farmland as well as opportunities at a farther distance given the reduced hauling expense.
Renewable energy: Biosolids have a heating value similar to a low-grade coal, allowing thermal dryer systems to process biosolids into a renewable thermal energy fuel and with further processing, generation of biochar, or concentrated minerals.
PFAS: While thermal drying alone won’t destroy PFAS and meet potential regulations, it is a precursor for next steps for destruction and compliance. Taking this pre-emptive step can set a facility up for the flexibility to adjust for compliance requirements.
2 real-world examples
How are the benefits of thermal drying realized in practice? Here are two real-world examples of facilities using thermal drying to enhance their operations and outcomes.
North Shore Water Reclamation District
North Shore Water Reclamation District’s (NSWRD) offsite, contracted-operated dryer facility has the capacity to process 32 dry tons of solids per day from its three WRFs. It is one of a handful of dryer facilities in the United States that dries wastewater solids without an upfront anaerobic digestion step. Anaerobic digestion conditions and homogenizes wastewater solids, making the product easier to dry and less odorous, but represents a large capital investment.
As part of the district’s Biosolids Master Plan, BC worked with NSWRD and its operating partner to baseline the facility’s operation and compare it to future operational scenarios, including several options for anaerobic digestion implementation. While the district established a strong operational program and added functionality over the years to mitigate the difficulties encountered with drying undigested solids, the feedstock properties showed a deleterious impact on the heat exchanger’s process efficiency, limiting the facility’s ability meet future growth demands.
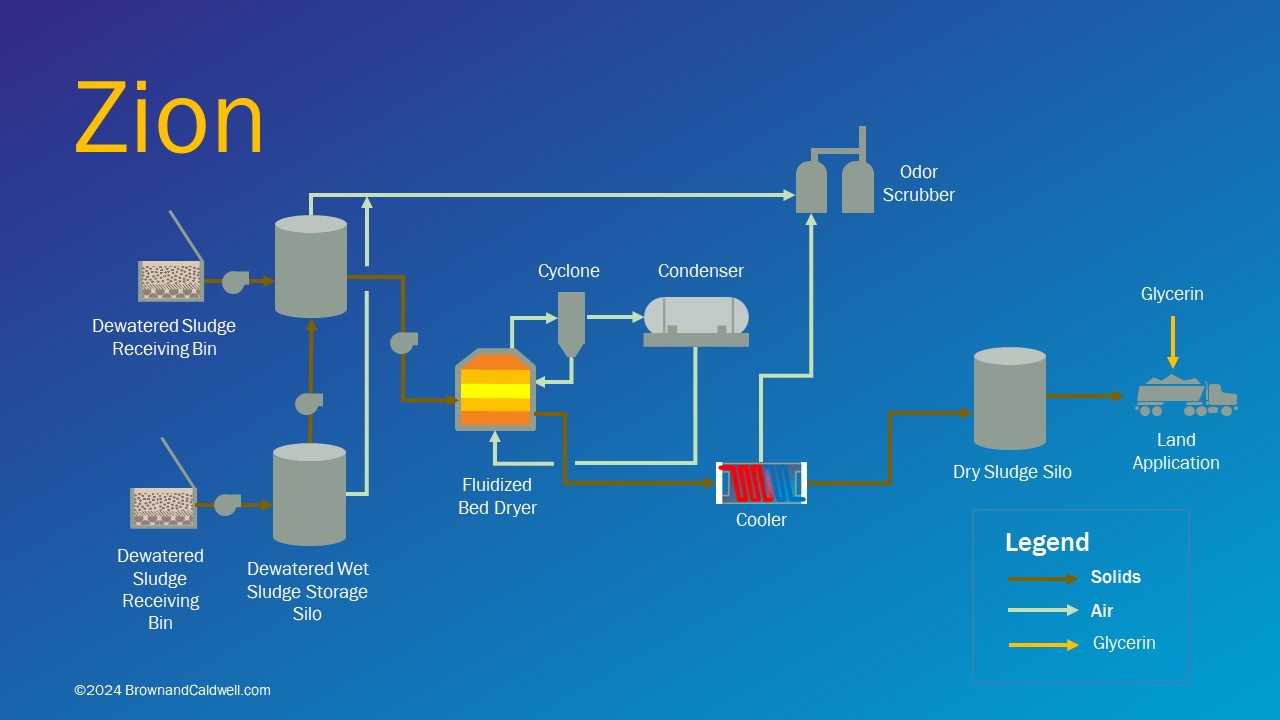
BC worked with NSWRD to baseline NSWRD’s existing dryer operation (shown here), compare it to future loading projections, and develop a holistic solution to meet the facility needs with upstream digestion to unlock existing dryer capacity. BC outlined a set of long-term improvements to implement new thermal drying and processing technology and triggers to determine timing.
BC worked with NSWRD to develop an implementation plan for anaerobic digestion that was right-sized to address operational challenges at the dryer, optimizing its cost-benefit. NSWRD’s larger adaptive biosolids management plan now includes the digestion project. The plan also features recommendations for succession planning for the dryer facility after it reaches the end of its useful life as well as programmatic drivers such as when PFAS regulations warrant installation of alternative thermal processes, providing NSWRD with an adaptive decision map to proactively set the course for the facility’s future.
Nashville Metro Water Services
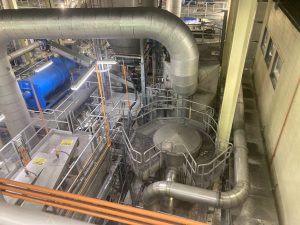
Operator-friendly design is key to BC’s design approach. Inclusion of a simple platform makes a more ergonomic friendly environment that allows regular maintenance activities to be accomplished safely.
Metro Water Services (MWS) in Nashville has instituted several optimization projects at its drying facility that have improved process performance and increased digester gas utilization.
One such project is its Central WRF optimization project, which BC Managing Principal, O&M Consulting, Ken Schnaars helped to commission in 2008 (Schnaars continues to serve as a long-term operations partner, taking a hands-on approach to refresher training, equipment, and optimization projects).
Within that facility is a pair of rotary drum dryers that can process 55 dry ton per day. The drum dryers produce a high-quality final pellet that MWS proudly markets as Music City Gold throughout the greater Nashville area and surrounding region.
Most recently, BC partnered with MWS as the Owner’s Agent to construct several facility enhancements, including expanded dryer access platforms, a temperature-controlled pellet loadout control room, and a dryer condensate solids recovery system.
Watch to see how Nashville Metro Water Services has upgraded its Central Water Reclamation Facility to treat an additional 100 million gallons per day of peak wet weather flow while also making it a safer, more reliable, and energy-efficient community asset.
MWS and BC incorporated these optimization measures, as well as other process insights, into a recent design of a new drum dryer facility at the Dry Creek WRF. The new Dry Creek dryers will allow MWS to dry biosolids produced from all of its WRFs, consolidating the biosolids management program to into a single product line, streamlining program oversight, and increasing operational resilience.
A solution that makes the most with less
As NSWRD and MWS show, thermal drying can address waste management challenges as well as enhance resource recovery and promote more eco-friendly wastewater treatment byproduct utilization. By making the most out of less waste, thermal drying is a biosolids management solution that provides immediate and future benefits for utilities.